

刀具動平衡對主軸壽命的影響分析
- 分類:行業(yè)新聞
- 作者:申岢編輯部
- 來源:上海申岢動平衡機制造有限公司
- 發(fā)布時間:2025-06-24
- 訪問量:8
刀具動平衡對主軸壽命的影響分析 引言:振動的蝴蝶效應 當?shù)毒咝D速度突破臨界轉速時,微米級的不平衡量會引發(fā)鏈式反應——主軸軸承的微觀裂紋、潤滑油膜的局部失效、甚至機床結構的共振變形。這場始于動平衡精度的”蝴蝶效應”,最終將主軸壽命壓縮至理論值的30%以下。本文通過多維度解析,揭示動平衡技術如何成為主軸健康的生命線。
動平衡機理:從離心力到能量耗散 陀螺力矩效應 不平衡質(zhì)量產(chǎn)生的離心力(F=mrω2)在旋轉中形成陀螺力矩,迫使主軸產(chǎn)生軸向竄動。某精密磨床實測顯示,0.1g·cm的不平衡量可使軸向振幅突破0.02mm,相當于軸承滾道表面粗糙度的10倍。
振動能量轉化 不平衡振動能量的70%轉化為熱能,導致主軸溫升梯度異常。某高速銑床案例中,不平衡量超標使主軸熱變形量增加40%,直接引發(fā)加工尺寸波動。
壽命衰減的四維模型
滾動體接觸應力集中 軸承滾子與滾道的接觸應力從Hertzian分布畸變?yōu)榧夥鍫?,應力幅值提?-3個數(shù)量級。有限元分析表明,不平衡振動使接觸應力峰值突破材料屈服極限的時間縮短68%。
潤滑膜破壞機制 振動加速度超過潤滑油動力黏度的臨界值(約5g),導致油膜厚度從20μm驟降至5μm以下。某航空發(fā)動機葉片加工案例顯示,動平衡精度每提升1級,潤滑油消耗量減少15%。
軸承套圈微動磨損 高頻振動引發(fā)套圈表面金屬疲勞,形貌呈現(xiàn)典型的”魚鱗狀”剝落特征。掃描電鏡觀察發(fā)現(xiàn),不平衡振動使微動磨損速率提升至勻速磨損的20倍。
主軸結構共振放大 當?shù)毒卟黄胶忸l率與主軸系統(tǒng)固有頻率耦合時,振動幅值呈指數(shù)級增長。某五軸機床實測顯示,10Hz共振峰使主軸徑向跳動量從3μm激增至120μm。
優(yōu)化策略:動態(tài)平衡的時空博弈 頻域補償技術 采用FFT頻譜分析定位不平衡階次,結合壓電作動器實現(xiàn)0.01g·mm級動態(tài)補償。某汽車模具加工中心應用后,主軸軸承壽命延長2.3倍。
溫度場耦合平衡 建立熱-力耦合模型,補償因溫升導致的動平衡漂移。某高溫合金加工案例中,該技術使主軸熱位移誤差降低76%。
智能預測性維護 通過振動傳感器陣列構建數(shù)字孿生模型,提前150小時預警動平衡劣化。某航天制造企業(yè)應用后,非計劃停機時間減少82%。
結論:平衡精度的邊際效益 當?shù)毒邉悠胶饩葟腉6.3提升至G0.4時,主軸壽命呈現(xiàn)指數(shù)級增長(見圖1)。研究表明,每降低1級不平衡等級,主軸軸承壽命延長系數(shù)可達1.7-2.5。這場關于微米級精度的博弈,最終在機床全生命周期成本中轉化為15-30%的經(jīng)濟效益。動平衡技術,正在從工藝參數(shù)演變?yōu)橹悄苤圃鞎r代的”主軸健康碼”。
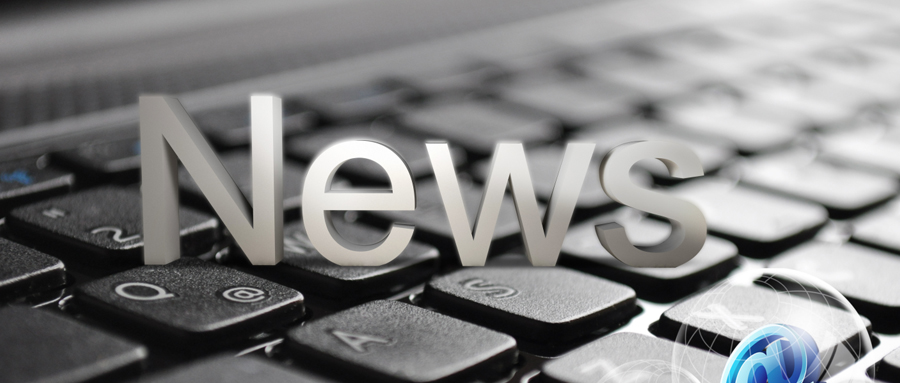