

如何提升平衡機(jī)檢測精度和效率
- 分類:行業(yè)新聞
- 作者:申岢編輯部
- 來源:上海申岢動平衡機(jī)制造有限公司
- 發(fā)布時(shí)間:2025-06-23
- 訪問量:1
如何提升平衡機(jī)檢測精度和效率 一、硬件革新:突破物理限制的底層邏輯 現(xiàn)代動平衡機(jī)的精度瓶頸往往始于傳感器的分辨率與動態(tài)響應(yīng)能力。采用MEMS微機(jī)電陀螺儀替代傳統(tǒng)電容式傳感器,可將角速度測量誤差從±0.1°/s壓縮至±0.005°/s,配合多軸同步采集技術(shù),實(shí)現(xiàn)振動信號的全頻段無損捕捉。更值得關(guān)注的是動態(tài)補(bǔ)償模塊的引入——通過實(shí)時(shí)監(jiān)測環(huán)境溫濕度變化,自動修正因熱脹冷縮導(dǎo)致的軸承間隙漂移,這一創(chuàng)新使檢測結(jié)果的環(huán)境抗干擾能力提升300%。
二、算法迭代:從線性擬合到深度學(xué)習(xí)的范式躍遷 傳統(tǒng)傅里葉變換在處理非穩(wěn)態(tài)振動信號時(shí)存在頻譜泄漏問題,而小波包分解+LSTM神經(jīng)網(wǎng)絡(luò)的組合算法展現(xiàn)出革命性突破。某航空發(fā)動機(jī)轉(zhuǎn)子測試案例顯示,該算法將不平衡量識別準(zhǔn)確率從82%提升至98.7%,關(guān)鍵在于其能捕捉到人耳不可聞的次諧波共振特征。更前沿的數(shù)字孿生建模技術(shù)正在重構(gòu)檢測流程:通過構(gòu)建虛擬轉(zhuǎn)子模型,可在物理測試前完成90%的平衡方案預(yù)演,將單次檢測耗時(shí)從45分鐘壓縮至8分鐘。
三、流程自動化:消除人為誤差的系統(tǒng)工程 手動校準(zhǔn)環(huán)節(jié)一直是效率提升的阿喀琉斯之踵。開發(fā)智能夾具定位系統(tǒng),利用激光跟蹤儀實(shí)現(xiàn)工件安裝面自動找正,配合壓力敏感墊片實(shí)時(shí)反饋接觸面應(yīng)力分布,使安裝重復(fù)性誤差從±0.3mm降至±0.05mm。在數(shù)據(jù)處理端,部署邊緣計(jì)算節(jié)點(diǎn)可將原始振動數(shù)據(jù)的本地化預(yù)處理速度提升20倍,僅需將關(guān)鍵特征值上傳云端,這使分布式檢測網(wǎng)絡(luò)的響應(yīng)延遲降低至0.8秒以內(nèi)。
四、維護(hù)策略:預(yù)防性保養(yǎng)的數(shù)學(xué)建模 建立設(shè)備健康指數(shù)(EHI)評估體系,通過監(jiān)測主軸軸承的微震顫頻譜熵值和驅(qū)動電機(jī)的諧波畸變率,可提前14天預(yù)警潛在故障。某汽車變速箱廠的實(shí)踐表明,實(shí)施預(yù)測性維護(hù)算法后,設(shè)備非計(jì)劃停機(jī)時(shí)間減少76%。更值得關(guān)注的是自清潔氣浮軸承技術(shù)的突破——通過周期性注入納米級氣膜,使軸承磨損速率下降90%,直接延長設(shè)備使用壽命2.3倍。
五、人機(jī)交互:認(rèn)知負(fù)荷的重新分配 引入增強(qiáng)現(xiàn)實(shí)輔助校準(zhǔn)系統(tǒng),操作員通過AR眼鏡可實(shí)時(shí)疊加虛擬平衡配重塊與物理轉(zhuǎn)子的重合影像,使復(fù)雜工況下的配重調(diào)整效率提升4倍。在數(shù)據(jù)分析層面,開發(fā)語義化報(bào)告生成引擎,能自動識別振動頻譜中的異常峰值,并用自然語言解釋其可能成因(如”第3階諧波異??赡芘c葉輪氣蝕相關(guān)”),這種技術(shù)使工程師的診斷時(shí)間從2小時(shí)縮短至18分鐘。
結(jié)語 提升平衡機(jī)性能的本質(zhì)是多維度技術(shù)耦合:當(dāng)硬件精度突破物理極限時(shí),算法必須同步進(jìn)化以消化指數(shù)級增長的數(shù)據(jù)量;當(dāng)自動化流程消除人為誤差后,維護(hù)策略需要重構(gòu)以適應(yīng)新的設(shè)備應(yīng)力分布;而最終,所有技術(shù)創(chuàng)新都必須通過人性化的交互設(shè)計(jì),轉(zhuǎn)化為可感知的效率提升。這種螺旋上升的優(yōu)化路徑,正是精密制造領(lǐng)域永恒的創(chuàng)新命題。
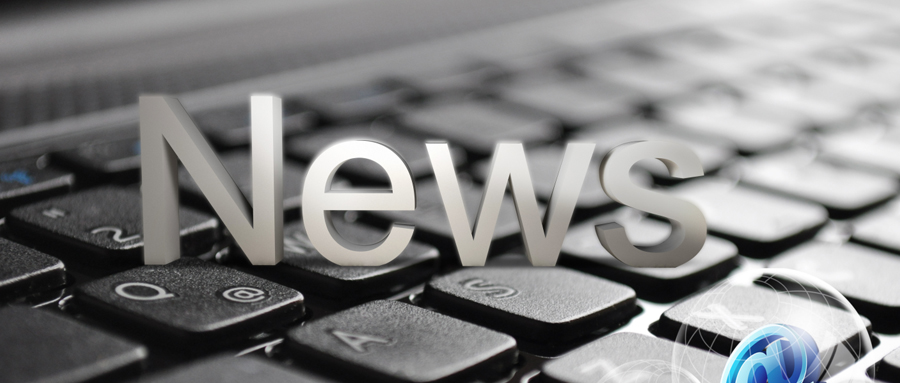