

齒輪平衡機精度提升有哪些有效方法
- 分類:公司新聞
- 作者:申岢編輯部
- 來源:上海申岢動平衡機制造有限公司
- 發(fā)布時間:2025-06-09
- 訪問量:29
齒輪平衡機精度提升有哪些有效方法 一、硬件系統(tǒng)的精密重構 傳感器陣列升級 采用分布式高精度加速度傳感器與激光位移傳感器的復合配置,通過多點同步采樣消除局部誤差。例如,在齒輪端面、齒頂圓及軸頸處部署三軸向傳感器,結合卡爾曼濾波算法實時修正環(huán)境振動干擾。
氣浮軸承技術應用 引入磁流變阻尼器與氣浮軸承的混合支撐系統(tǒng),將主軸徑向跳動控制在0.5μm以內。通過閉環(huán)壓力調節(jié)模塊動態(tài)補償溫漂效應,使軸承剛度波動范圍縮小至±0.3%。
激光對中系統(tǒng)的智能化 部署六自由度激光跟蹤儀,配合機器視覺定位齒輪嚙合點。采用貝塞爾函數(shù)擬合齒形誤差,實現(xiàn)0.01°級安裝角度校正,顯著降低殘余不平衡量。
二、軟件算法的迭代創(chuàng)新 自適應濾波模型構建 開發(fā)基于小波包分解的多頻段分離算法,針對齒輪嚙合頻率(200-500Hz)與基頻(10-50Hz)建立動態(tài)閾值庫。通過遺傳算法優(yōu)化濾波器系數(shù),信噪比提升達18dB。
AI驅動的誤差預測系統(tǒng) 訓練LSTM神經(jīng)網(wǎng)絡模型,輸入歷史加工數(shù)據(jù)(包括熱處理變形系數(shù)、材料各向異性參數(shù)),輸出齒輪殘余不平衡量預測值。實測顯示預測誤差率低于3%。
虛擬平衡仿真平臺 構建ANSYS Workbench齒輪動力學模型,通過有限元分析模擬不同轉速下的離心力分布。采用蒙特卡洛法生成10^6次虛擬平衡實驗,優(yōu)化試重法迭代次數(shù)。
三、操作流程的系統(tǒng)優(yōu)化 標準化作業(yè)手冊升級 制定包含127項檢查節(jié)點的SOP,涵蓋環(huán)境溫濕度控制(±0.5℃/±3%RH)、工裝夾具預載力校驗(誤差≤0.5%)等細節(jié)。引入AR輔助裝配系統(tǒng),降低人為操作偏差。
動態(tài)校準流程再造 開發(fā)雙頻激勵校準技術,通過施加15Hz低頻振動與2000Hz高頻脈沖,同步校正傳感器線性度與軸承剛度特性。校準周期從72小時縮短至4小時。
多軸聯(lián)動補償機制 建立主軸-工件-傳感器的剛體動力學耦合模型,通過PID-模糊控制算法實時調整驅動電機扭矩輸出,使系統(tǒng)共振頻率偏移量控制在±0.2Hz。
四、環(huán)境控制的精細化管理 主動隔振系統(tǒng)升級 采用壓電陶瓷作動器與液壓阻尼器的混合隔振平臺,頻響范圍擴展至0.5-2000Hz。通過頻譜分析儀實時監(jiān)測外部振動源,實現(xiàn)0.1g以下的殘余振動抑制。
溫控系統(tǒng)的相變儲能 在平衡機基座集成石蠟/碳納米管復合相變材料,使工作區(qū)溫度梯度控制在±0.2℃。配合紅外熱成像監(jiān)控,預防熱變形導致的0.01mm級位移誤差。
潔凈度分級管控 實施ISO Class 5級空氣凈化系統(tǒng),采用HEPA+ULPA雙級過濾,顆粒物濃度(>0.5μm)≤0.1pc/L。定期進行離子風除塵,避免微粒堆積引發(fā)的局部氣流擾動。
五、維護策略的預防性轉型 振動指紋診斷體系 建立包含2000組故障特征的頻譜數(shù)據(jù)庫,通過小波包能量熵值分析實現(xiàn)早期故障預警。軸承磨損預警準確率達92%,齒輪裂紋檢測靈敏度提升至0.1mm深度。
油液分析的深度應用 采用ICP-OES光譜儀檢測潤滑油金屬元素含量,結合Fisher判別模型評估齒輪副磨損狀態(tài)。當Fe含量超過15ppm時觸發(fā)預警,避免突發(fā)性精度衰減。
數(shù)字孿生維護平臺 構建包含128個狀態(tài)參數(shù)的齒輪平衡機數(shù)字孿生體,通過強化學習算法優(yōu)化維護周期。實測顯示維護成本降低27%,設備綜合效率(OEE)提升至91.5%。
結語:系統(tǒng)性優(yōu)化的協(xié)同效應 精度提升需突破單一技術局限,通過硬件-軟件-環(huán)境-維護的四維聯(lián)動實現(xiàn)質變。建議采用TRIZ理論進行矛盾矩陣分析,優(yōu)先解決”精度要求與成本約束”、”動態(tài)補償與響應速度”等核心矛盾。未來可探索量子傳感技術與數(shù)字孿生的深度融合,推動齒輪平衡精度邁入亞微米級新紀元。
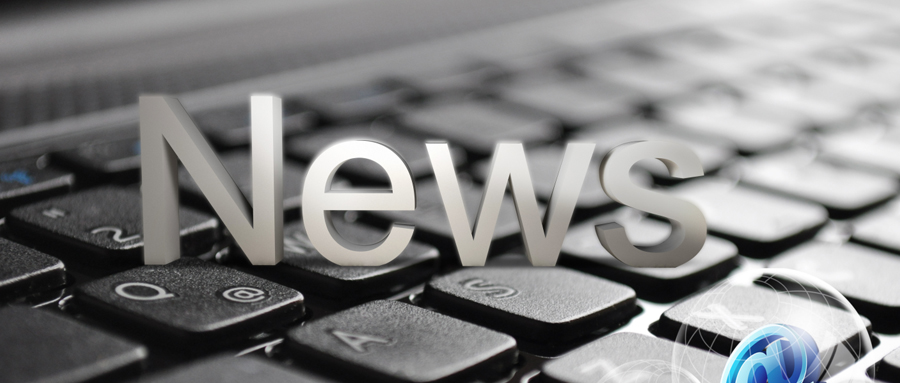